Valentine’s Day is a time to recognize the perfect partner in your life. So we thought, why not take a moment to celebrate the match of Laser Cutting + Press Brake forming. So what makes this such a good match? Fast, efficient, & clean laser cutting + automated press brake bending means we can manufacturer parts faster with more accuracy and provide an often cheaper alternative to Roll Forming. Don’t worry Roll Forming still has its own perfect match!
A World of Difference- Laser Cutting + Press Brake:
In early 2019, we purchased a 3-kW Mazak Optiplex Champion 3015 fiber laser cutting machine and a SafanDarley 100T electric press brake. We choose to invest in this technology because we knew how well they would complement each other in the shop for years to come.
In fact, it was such a great match that within 6 months we purchased another 8-kw Mazak fiber laser through our distributor, Capital Machine Technologies.
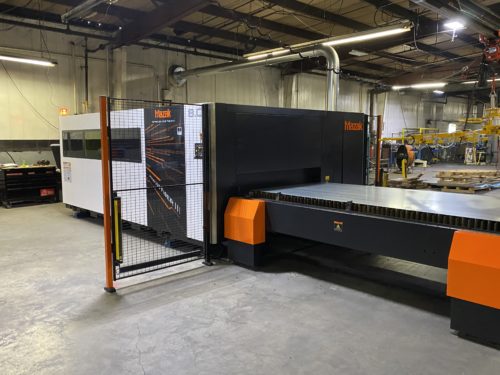
8kw Mazak Fiber Laser at USMC
Press Brake Keeping Pace:
Even with the laser cutting speed of our two Mazak Fiber Lasers, the SafanDarley press brake can keep up with the bending work. General Manager Mike Hansen describes just how the press brake is able to keep up: “When we have the parts that are coming off the laser as fast as they’re coming off, we need something that can do multiple bends on them very quickly. The press brake with fully automated gauging can do this,” Hansen said. “We’re not having a bunch of downtime or setting up multiple machines to run multiple bends, and we do it much more efficiently because everything is computerized. It also allows us to bend with a lot more accuracy.”
Shaun Reiff, of Capital Machine Technologies, describes how the SafanDarley press brake utilizes state of the art technology to handle multiple detailed bends:
“Bending jobs are created with an offline software package called AutoPOL. The brake uses this data to illuminate the LED lights on the upper and lower tool clamping system. These LED lights, part of the brake’s Smart Tool Locator, indicate precisely where on the press brake the tools need to be loaded in the machine to run every job.
When the job is ready for the press brake, all the operator has to do is call it up, load the appropriate tools, and form the part. The process of loading a program, loading the tools, and running a part that meets quality specs typically can be done in less than five minutes.”
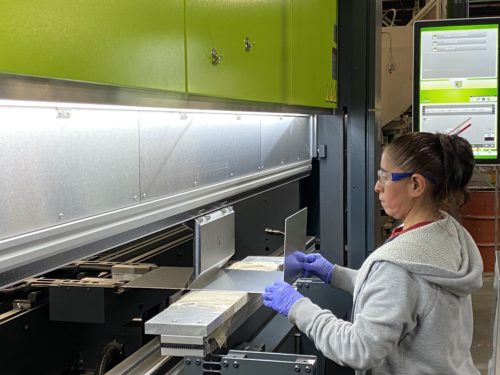
SafanDarley Press Brake Operator
By having machinery that is both user-friendly and technically advanced we have been able to serve the growing customer demand for laser cutting and press brake work and can easily accommodate additional shifts to ensure we deliver on-time with accuracy.
Automating Manufacturing:
The addition of this modern fabricating equipment has set us up to get parts out the door on-time and according to specs. As a supplier to OEMs, we often have long receptive runs of parts and components spanning throughout the year. “The great thing about the laser and the press brake is once the files are in there, you only need to create the program once,” Hansen said. “If it’s a repetitive part, you can just call it up and hit go.” Once we have done one run of a part the next run can be processed even faster.
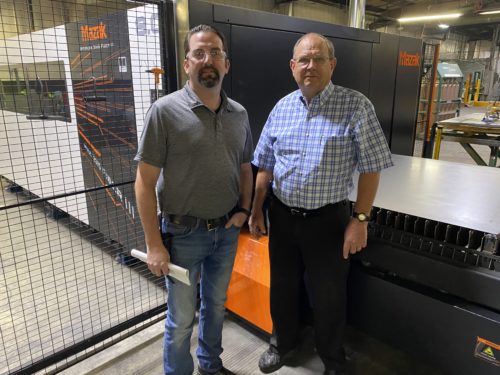
Our President, Steve McDaniel & General Manager, Mike Hansen- Another “Perfect Match!”
Contact us to learn more about this perfect match.
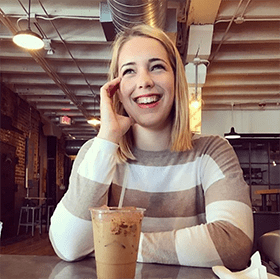
As the Marketing Manager at US Metal Crafters, Meredith Barnes is fully immersing herself in all things metal. Self-ascribed google search addict and chronic researcher; she’s discovering the world of metal crafting one Latte at a time. Follow along on her journey to metal here.